Lyngdorf Audio’s most powerful amplifier undergoes intense 24-hour burn-in testing
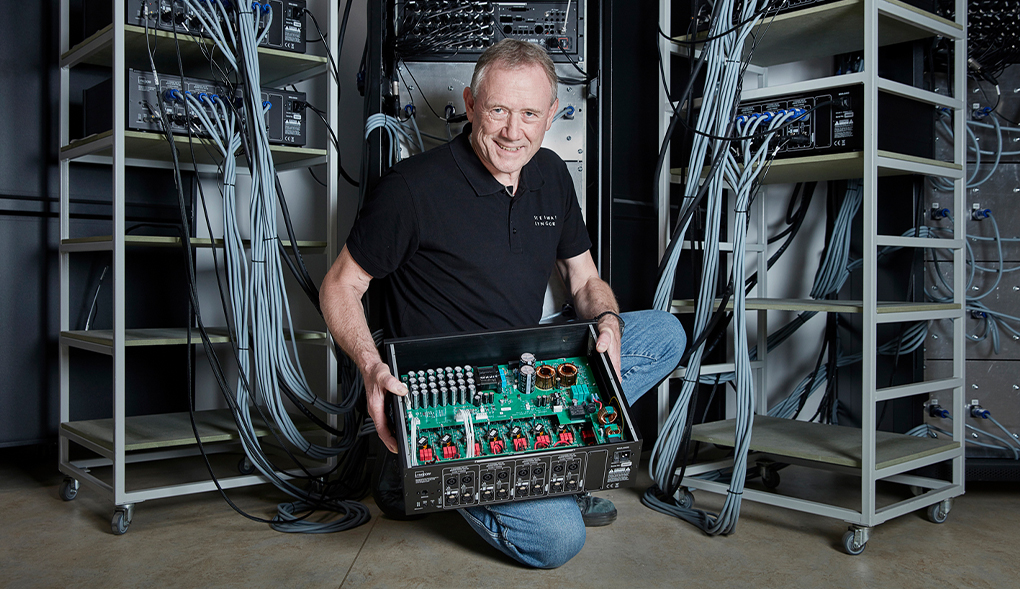
Picture by Kåre Viemose, www.viemose.dk
The task
In 2024, Steinway Lyngdorf in Skive launched the Lyngdorf MXA-8400 – an eight-channel power amplifier for home theaters and music systems. The amplifier is the most powerful product the company has ever produced. The class D amplifier delivers 400 watts in four ohm in all eight channels – 3,200 watts in total. And with a suggested retail price of DKK 66,999 / 8.999,- Euro customers expect sound from the top shelf. That’s why every single amplifier goes through a “burn-in” test for 24 hours, where components and circuits are stress tested for faults. The performance is then tested in a series of performance tests that measure noise and harmonic distortion before the amplifier is packed and shipped to dealers and customers.
Senior PTA/service technician Gert Wegeberg Amby has been responsible for the development of the test setup for the amplifier. It includes everything from software scripts, that automates the tests, to test cabinets and unique self-created solutions, which Gert Wegeberg Amby himself invents, when no other solutions exist.
The solution
“The amplifier is our most powerful product to date and it draws all the power of an household outlet that it possibly can. When we do burn-in tests, we have 12 amplifiers running at the same time over 24 hours – and all times at full throttle. We had to redesign our power system to be able to cope, so we have one socket per appliance,” says Gert Wegeberg Amby.
The amplifiers are developed and manufactured in Skive, but the printed circuit boards are made at Lyngdorf Audio’s long-term suppling partner in Thailand. To ensure that the individual boards are tested correctly, Gert Wegeberg Amby has developed the test equipment and authored test manuals, which carefully outlines the test procedure.
The three test cabinets used during burn-in of the MXA-8400 stand side by side. At the bottom of the cabinets are four fans that provide air cooling, and the rest of the cabinet is full of so-called loads – powerful resistors connected to all eight amplifier speaker terminals. Each of the three cabinets handles four amps during the 24 hours long burn-in process.
“When the burn-in is running, it gets very warm in this closet. Four times 3,200 watts is used when it is operating, it’s like walking up to a wood-burning stove,” says Gert Wegeberg Amby.
During burn-in, the amplifiers are tested with various sound files, and in the absence of ready-made solutions Gert Wegeberg Amby had to build his own “sound card”, that sends the same audio file from a laptop to four amplifiers. Here come his inventive skills into account.
After burn-in, the amplifier’s sound performance is tested. Distortion, signal to noise ratio, operating temperatures and several other parameters are checked, and all data for the individual amplifier are stored in log files on a server. Should an error occur on an amplifier at the customer later, the log file can always be searched for on the amplifier’s serial number. After testing, the amplifier is ready to be packed. But how does such an amplifier sound then?
“It must be someone else’s job to tell how good it is. But you’ll get the sound out that you put into it. It’s not the amplifier that is the limitation, that’s for sure,” says Gert Wegeberg Amby.
Read the original article (in Danish) in the Danish magazine Teknikeren here.